Step
1
Tool & Part design
Product industrialization, we work together with the customer to create the best final result.
3D design during the different steps, we continue working side by side with the customer. Each mold is equipped with its own “Technical Book”, containing complete information about its application and the certificates regarding the material used and the treatments performed.
FEM Analysis, Simulations,
Tool Virtualization to predict its useful life.
Virtualization of the Die Casting Process (TPV).
We design tools with innovative features:
• Dosing system analysis • Ejection force
• Tool heat treatment analysis •Trimming tool study •Burst test study
Software:
• Ansys
• Magma
• ProCast
Possibility to run FEM analysis combining predicted defects and residual stress generated by the die casting process.
Step
2
PROCESSES VIRTUALIZATION
Step
2
PROCESSES VIRTUALIZATION
FEM Analysis, Simulations,
Tool Virtualization to predict its useful life.
Virtualization of the Die Casting Process (TPV).
We design tools with innovative features:
• Dosing system analysis • Ejection force
• Tool heat treatment analysis •Trimming tool study •Burst test study
Software:
• Ansys
• Magma
• ProCast
Possibility to run FEM analysis combining predicted defects and residual stress generated by the die casting process.
Step
3
CNC MACHINING
Precision manufacturingwith cutting edge machines with3 or 5 axis.
Zero point clamping systems in every CNC machine. All technical parameters of the cutting tools are set by our CAM department.
3 spark erosion machines
1 wire erosion machine
Advanced co-design allows us to realize elements with complex profiles. In-house manufacturing of the electrodes.
Step
4
Erosion
The customization of the EDM machines electronic parameters allows a shortening in terms of machining time and electrode wear while guaranteeing the quality of the treated surfaces.
Step
4
Erosion
The customization of the EDM machines electronic parameters allows a shortening in terms of machining time and electrode wear while guaranteeing the quality of the treated surfaces.
3 spark erosion machines
1 wire erosion machine
Advanced co-design allows us to realize elements with complex profiles. In-house manufacturing of the electrodes.
Step
6
QUALITY CONTROLS
Photometric control of all active parts is carried out through best fitting activities at the end of each manufacturing step. This permits to shorten the assembly times.
FAIST TOOL SHOP
FAIST Light Metals Engineering srl is a high pressure die casting company supporting all the foundries of FAIST Group, in every application sector. Our technicians follow the entire manufacturing process from the mold design to the final product, this allows us to create efficient and reliable molds.
FAIST Light Metals Engineerig s.r.l.
Via Stelloni Ponente 33 - 40012
Calderara di Reno (BO)
ITALY
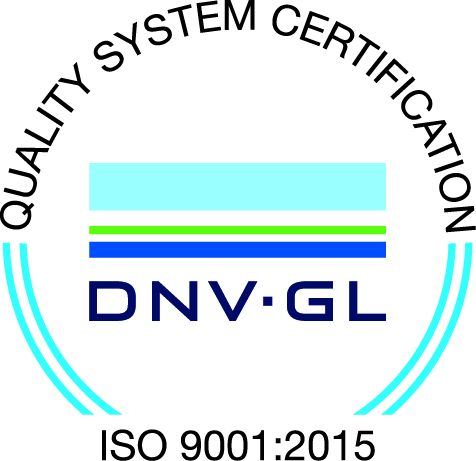
WRITE HERE your message
CONTACT US
Call
Phone: +39 051 722 122
Write us a message
Email: info@faisttoolshop.com